When it comes to dismantling and recycling wind turbines, the discussion revolves around one component in particular: the rotor blade. While steel towers, concrete foundations, and copper cables are comparatively easy to recycle, rotor blades are much more complex and are made of different materials, making them significantly more difficult to recycle.
The largest part of a rotor blade is made of glass and carbon fiber reinforced plastics (GFRP and CFRP), which are also firmly bonded to other materials. The shells of the rotor blade are constructed as a sandwich: fiber composites, balsa wood and PET or PVC foam form a solid construct. The spar caps are made exclusively of GFRP or CFRP. The prerequisite for true recycling is therefore first of all clean separation of these materials. The main challenge here is to separate the glass and carbon fibers from the surrounding epoxy resin. Only then can they be recycled again in the same way.
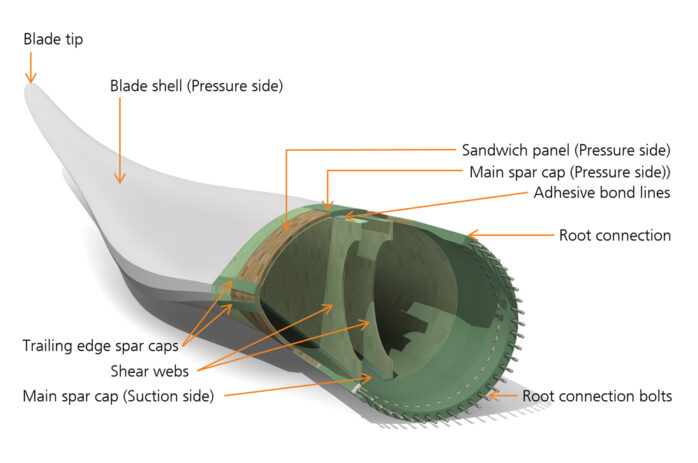
The challenge: recycling instead of downcycling
The methods for this already exist. There are various reasons why so few rotor blades are currently recycled:
- Many rotor blades are used after their calculated lifespan or sold for further use after dismantling. [1][2] They are therefore not (yet) in the recycling process.
- Separating the materials is energy-intensive and therefore expensive. The production of new glass fibers is significantly cheaper.
- Even though the estimated 83,000 tons [3] of rotor blade mass that will have reached the end of their planned life span by 2037 sounds enormous, it is actually a relatively small amount. In comparison: The city of Bremen had a household waste volume of 300,000 tons in 2021 [4] alone. The construction of sorting and recycling plants for rotor blades is therefore only economically viable if the processes are as energy-efficient and automated as possible and deliver high-quality residual materials.
Since 2009, rotor blades may no longer be disposed of in landfills in Germany. Other European countries have also already adopted such guidelines or are on the way to doing so. Even though in some cases rotor blades are used as playground equipment and bicycle shelters or converted into a bench to offer guests at the Fraunhofer IWES in Bremerhaven a comfortable place to sit, the usual disposal method is currently thermal recycling of the shredded rotor blades in the cement industry. Plastics and epoxy resin are incinerated to generate energy, while the ash from glass fibers is used as a raw material in cement. There is still a long way to go before we achieve genuine material recycling, i.e. the use of materials for new products or as raw materials. Furthermore, the CFRP content of modern rotor blades longer than 70 meters cannot be disposed of in this way due to the material characteristics. In a few years, this will become a new challenge.
A prerequisite for material recycling is to separate the materials of which the rotor blade is made. Balsa wood and foams are comparatively easy to separate mechanically and recycle, for example as building or insulating materials. The composites CFRP and GFRP, on the other hand, have to be separated from each other using pyrolysis, i.e. splitting by heat with a large exclusion of oxygen, or with a chemical dissolution, solvolysis. Currently, the result is always downcycling because the materials do not have the same properties as before.
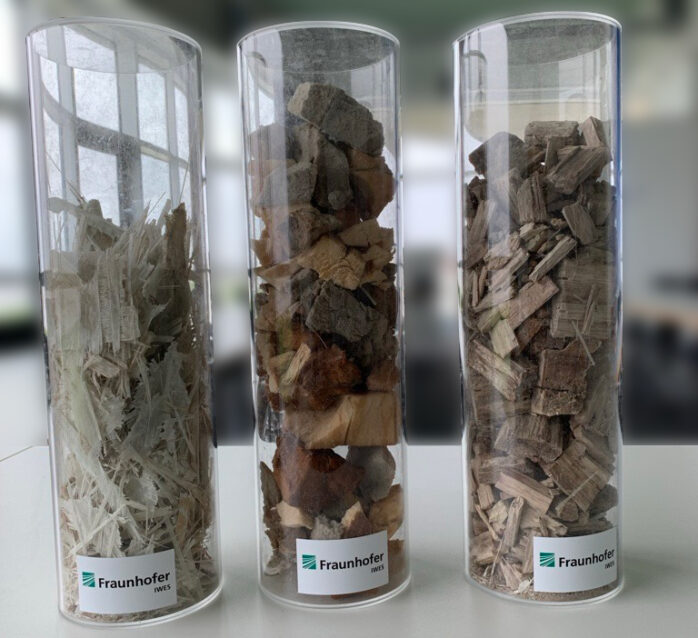
Research at Fraunhofer IWES: The concept is in place, individual steps are being optimized
The aim of the research at Fraunhofer IWES is to ensure high-quality recycling that preserves many of the fibers’ positive material properties. At the same time, energy consumption and thus CO2 emissions must be kept in mind. In the course of various consecutive research projects, Fraunhofer IWES has developed a concept for an economically viable disposal strategy for rotor blades and is examining individual methodical steps.
The recycling concept developed in the KoReNaRo project envisages the rotor blades first undergoing an “incoming goods inspection”: Hot air is blown into the blade so that a thermographic image can provide an accurate picture of the structure – this is important in order to prepare the disassembly precisely according to materials. The next step is mechanical disassembly: the full-laminate structures and sandwich components are separated so that they can be recycled using different methods. To separate the foam and balsa wood from the sandwich materials, these parts are coarsely shredded and separated using the sink-float method. The full-laminate structures, on the other hand, can be separated into oil, gas and pure fibers as raw materials using batch pyrolysis and then reused as starting materials for new processes and products.
Re Sort, Reusa Blade, and EoLO-HUBs: three projects, three approaches
In the Re Sort project, scientists from our Rotor Blades Department, under the project coordination of Fraunhofer IFAM, are investigating two pyrolysis processes: The batch pyrolysis to be developed in the project, in which the resin in the thick fiber composite components is decomposed into oily and, above all, gaseous hydrocarbon compounds by heating, and microwave pyrolysis, in which the energy is supplied by microwaves. The aim is to achieve an optimum balance between energy input and the quality of the recycled fibers. In this project, Fraunhofer IWES is responsible for the evaluation and testing of the recovered fibers. To do this, so-called coupons are produced from the recycled fibers, i.e. the fibers are re-bound with resin to form test plates. The quality of the plates is tested using mechanical tests (tension and bending).
Together with a rotor blade manufacturer and other project partners, the rotor blade department is investigating the use of solvolysis with acetic acid as an alternative chemical process to dissolve the epoxy resin in the ReusaBlade project. However, this method is only suitable for special resins, such as recyclamine. The focus is on the relationship between the speed of material degradation and the thickness and surface area of the test material. After initial tests on a laboratory scale, rotor blade parts such as flanges or sandwich elements are dissolved in a three-by-five-meter acid basin under industry-like conditions. The recovered fibers are then reprocessed and tested. A simulation developed in parallel, which is continuously compared and validated with the test results, should make such large-scale tests redundant in the future.
In the international joint project EoLO-HUBs, in which Fraunhofer IWES is participating, 20 partners from all over Europe are investigating the entire process chain from the disassembly of the rotor blades to the recovery of the fibers by pyrolysis and solvolysis to the meaningful use of the recycled materials. The focus is on three main areas: dismantling and pre-treatment of the blades, sustainable fiber recovery, and improving processes for refining the recovered fibers. By the end of the project in 2026, a demonstration recycling plant is to be set up in Spain and Germany, respectively, and the entire process from blade to new fiber is to be demonstrated.
Rotor blade recycling: challenges and solutions
From today’s perspective, it is not yet possible to say for sure which process and which approach will ultimately prevail. Many steps are still needed to organize an economically viable recycling solution. There will be different solutions for different users. In addition to the current projects, further research projects on the subject of recycling are planned at Fraunhofer IWES in order to continue research into sustainable and efficient recycling methods.
List of references
[1] Internationaler Marktplatz der windindustrie – wind-turbine.com
[2] Bundesnetzagentur, Marktstammdatenregister Erweiterte Einheitenübersicht | MaStR (German only)
[3] From the Institute for Energy, Recycling and Environmental Protection at Bremen Universtiy of Applied Sciences database developed in the RecycleWind project, expanded by Fraunhofer IWES.
[4] Freie Hansestadt Bremen, Abfallwirtschaftsplan und Abfallbilanzen Abfallwirtschaftsplan und Abfallbilanzen – Die Senatorin für Umwelt, Klima und Wissenschaft (German only)
Related article:
Might stick around: IWES tackles rotor blade production challenges with the Variable Glue Applicator